Welcome to our comprehensive guide on how to fix a leaking concrete water tank in New Zealand. Whether you’re a homeowner or a business owner, maintaining a functional water tank is crucial for ensuring a reliable water supply. In this blog post, we’ll delve into the common causes of leaks, how to identify them, and provide a detailed, step-by-step guide to repairing your tank effectively. By following our expert tips, you’ll not only extend the life of your tank but also prevent future issues. So, let’s get started on ensuring your water tank is leak-free and running efficiently!
To fix a leaking concrete water tank in New Zealand, first identify the leak by looking for visible cracks, damp patches, or unusual water loss. Ensure safety by wearing protective gear and emptying the tank. Clean the affected area thoroughly, removing any debris. For small cracks, apply a concrete patch mix; for larger cracks, use epoxy or polyurethane injections. After repairs, seal the tank with a waterproof sealant. Regular inspections and maintenance are crucial to prevent future leaks. If the damage is extensive, consider hiring a professional for repair.
Understanding The Problem
Common Causes of Leaks
Leaks can be a homeowner’s nightmare, leading to unnecessary expenses and potential damage if not addressed promptly. Understanding the root causes can help in preventing and managing leaks effectively. Here are some common culprits:
1. Cracks Due to Age and Weather: Over time, materials deteriorate, especially when exposed to harsh weather conditions. Prolonged exposure to sun, rain, and fluctuating temperatures can cause the tank’s material to crack and weaken, making it susceptible to leaks.
2. Poor Construction or Installation: Sometimes, the issue lies in the initial stages. If the construction or installation of the tank isn’t done correctly, it can lead to structural weaknesses. This includes using substandard materials, inadequate waterproofing, or improper sealing techniques, all of which can contribute to leaks.
3. Ground Movement and Seismic Activity: Natural ground movements and seismic activities can exert pressure on the tank, causing it to shift or crack. This is particularly relevant in regions prone to earthquakes or frequent ground settling, where the structural integrity of tanks can be compromised.
4. Chemical Reactions with Water and Soil: The chemical composition of the water and soil can react with the tank’s material. Over time, these chemical reactions can corrode the tank or cause other forms of degradation, leading to leaks. For instance, high acidity in water or soil can be particularly corrosive.
Identifying the Signs of a Leak
Detecting a leak early can save a lot of trouble and expense. Here are some telltale signs to watch out for:
1. Visible Cracks and Damp Patches: One of the most obvious signs of a leak is the appearance of cracks or damp patches on or around the tank. These can often be seen on the exterior surface and should be inspected regularly.
2. Reduced Water Levels Without Usage: If you notice a significant drop in water levels without corresponding usage, it’s a clear indicator that there might be a leak. Regular monitoring of water levels can help in early detection.
3. Mold or Algae Growth Around the Tank: The presence of mold or algae is a sign of excess moisture, which could be due to a leak. These organisms thrive in damp conditions, so their growth around the tank is a red flag.
4. Unusual Water Bills: A sudden spike in water bills without an increase in usage can also indicate a leak. This is because the water lost through the leak will still be recorded as usage, leading to higher bills.
Understanding these causes and signs of leaks can help in taking proactive measures to prevent and address them. Regular inspections and maintenance, along with prompt action when issues are detected, can save homeowners from the hassle and cost of dealing with extensive water damage.
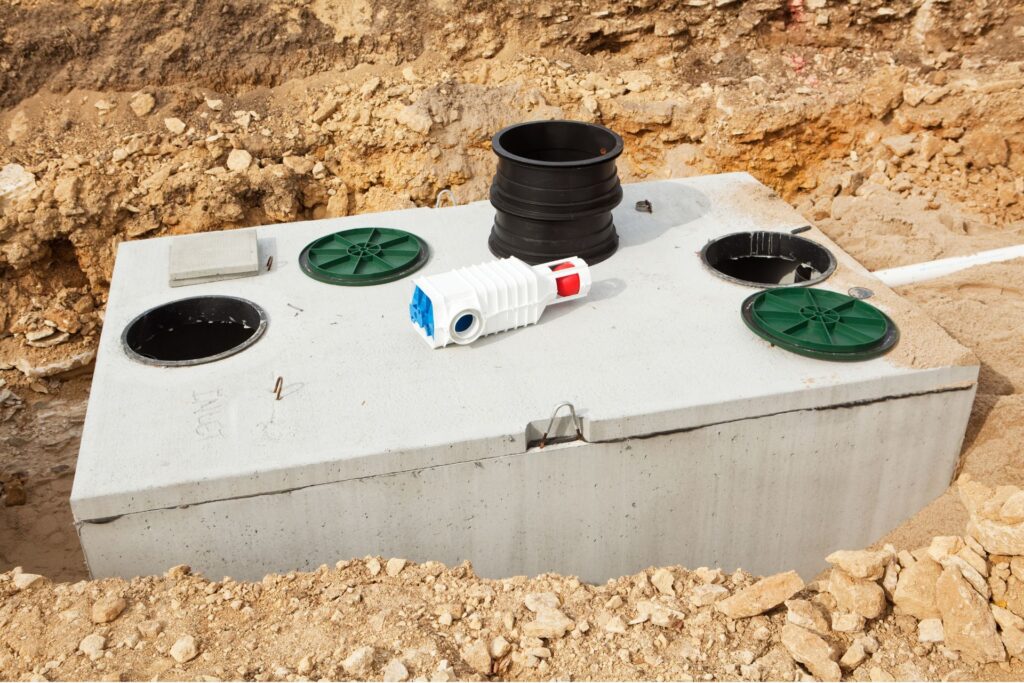
Preparing For The Repair
When embarking on a repair project, preparation is key to ensuring the job goes smoothly and safely. In this section, we’ll discuss the essential steps you need to take before starting any repair work, focusing on safety and the necessary tools and materials.
Safety First
Safety should always be your top priority when undertaking any repair task. Here’s why and how you should ensure a safe working environment.
Importance of Safety Gear
Before you even think about picking up a tool, make sure you have the proper safety gear. This includes:
Gloves: Protect your hands from sharp edges, rough surfaces, and harmful substances.
Goggles: Shield your eyes from debris, dust, and chemical splashes.
Dust Mask: Prevent inhalation of dust and fine particles, especially if you’re working with materials like concrete or wood.
Steel-Toed Boots: Protect your feet from heavy falling objects and provide a good grip.
Investing in quality safety gear can prevent accidents and injuries, allowing you to focus on the task at hand with peace of mind.
Ensuring the Tank is Empty and Dry
If your repair involves a tank, such as a water tank or fuel tank, it’s crucial to ensure it is completely empty and dry before you begin. Here’s how you can do it:
1. Drain the Tank: Make sure to remove all contents from the tank. This might involve siphoning out liquids or simply using the tank’s drainage system.
2. Dry the Interior: Use a cloth or air-dry the inside of the tank to ensure it is completely dry. Moisture can interfere with repair materials and create a hazardous working environment.
3. Ventilation: Make sure the area is well-ventilated to avoid the buildup of fumes, which can be both dangerous and unpleasant.
Taking these steps not only makes the repair process easier but also significantly reduces the risk of accidents.
Tools and Materials Needed
Having the right tools and materials at your disposal is critical for the success of your repair project. Here’s a comprehensive list of what you’ll need.
List of Essential Tools
1. Hammer: A versatile tool for breaking and shaping materials.
2. Chisel: Perfect for detailed work, such as removing old material or creating precise cuts.
3. Drill: Essential for making holes and driving screws, especially if you need to secure new parts.
4. Screwdrivers: Both flathead and Phillips screwdrivers are crucial for tightening or loosening screws.
5. Utility Knife: Handy for cutting through materials like plastic, rubber, and more.
Having these tools ready before you start ensures you won’t have to pause your work to look for what you need.
Materials Required
1. Concrete Patch Mix: Ideal for repairing cracks and holes in concrete surfaces. Make sure you follow the manufacturer’s instructions for the best results.
2. Sealant: This is essential for waterproofing and sealing joints and cracks. Choose a sealant suitable for the material you are repairing.
3. Sandpaper: Necessary for smoothing rough edges and preparing surfaces for patching or painting.
4. Cleaning Supplies: Before starting the repair, cleaning the area is crucial for proper adhesion of patch materials. Have some rags, brushes, and cleaning agents on hand.
By preparing all the tools and materials in advance, you can ensure that the repair process is efficient and effective. Not only does this save time, but it also helps you achieve a professional finish on your project.
In summary, preparing for a repair involves prioritizing safety and gathering the necessary tools and materials. By taking these steps, you set yourself up for a successful and safe repair process, ensuring that your project is completed to the highest standard.
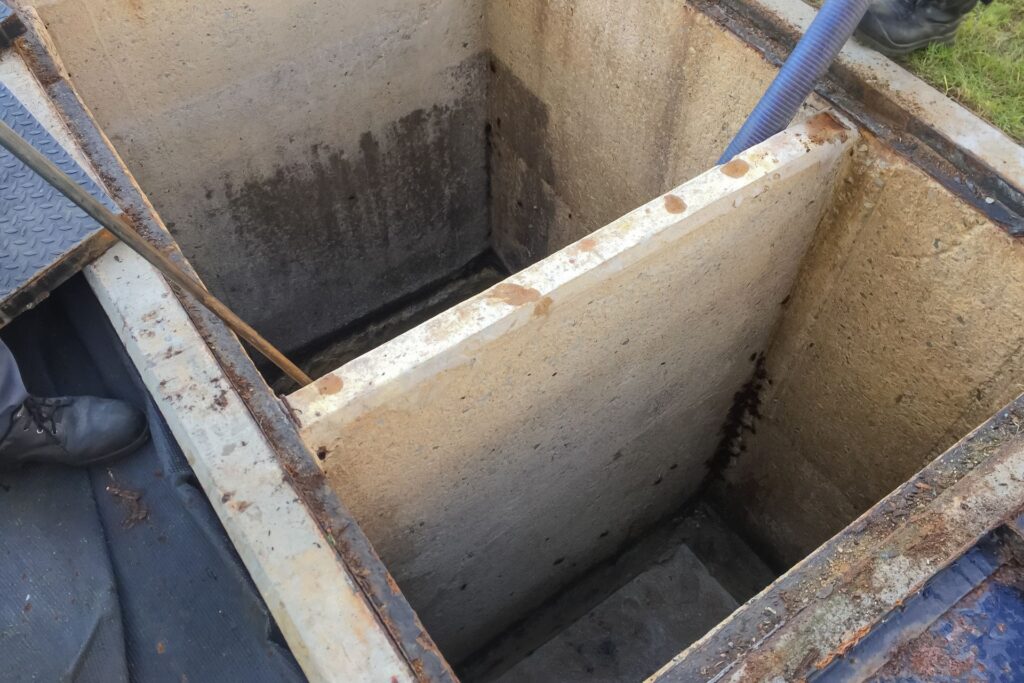
Step-By-Step Repair Guide
Repairing a crawl space foundation can seem like a daunting task, but breaking it down into manageable steps makes it much more approachable. Here’s a detailed, step-by-step guide to help you through the process.
Cleaning and Preparing the Area
Before you can start repairing cracks and holes in your crawl space foundation, it’s crucial to prepare the area properly.
1. Removing Debris and Loose Material from Cracks
Start by removing any debris, dust, or loose material from the cracks. Use a stiff brush, vacuum, or compressed air to ensure the area is clean. This step is vital because any debris left in the cracks can prevent the repair material from adhering properly.
2. Cleaning the Surface Thoroughly
Once the debris is cleared, clean the surface thoroughly. You can use a pressure washer or a hose with a high-pressure nozzle to wash away any remaining dirt and dust. Allow the area to dry completely before proceeding to the next step.
Fixing Small Cracks
Small cracks in your crawl space foundation are relatively easy to repair if you follow these steps:
1. Mixing the Concrete Patch Material
Choose a high-quality concrete patch material specifically designed for small cracks. Follow the manufacturer’s instructions to mix the patch material. Typically, this involves adding water to a dry mix and stirring until you achieve a smooth, paste-like consistency.
2. Applying the Patch to Small Cracks
Using a putty knife or trowel, apply the mixed patch material to the cracks. Press the material firmly into the cracks to ensure it fills all voids.
3. Smoothing and Allowing It to Set
Smooth the surface of the patch with the putty knife or trowel. Make sure the patch is level with the surrounding surface. Allow it to set and cure according to the manufacturer’s instructions, usually for at least 24 hours.
Repairing Larger Cracks and Holes
Larger cracks and holes require more extensive repair techniques:
1. Chiseling Out Larger Cracks to Create a Clean Surface
For larger cracks, use a cold chisel and hammer to widen the crack and create a clean, rough surface. This helps the repair material bond better. Make sure to remove any loose material.
2. Using Epoxy or Polyurethane Injection for Deeper Cracks
For deeper cracks, epoxy or polyurethane injections work best. These materials can penetrate deep into the cracks and provide a strong bond. Follow the product instructions for mixing and applying the injection material.
3. Applying Hydraulic Cement for Larger Repairs
If the cracks or holes are significantly large, hydraulic cement is a suitable option. Mix the hydraulic cement according to the manufacturer’s instructions and apply it to the prepared surface. Hydraulic cement sets quickly, so works efficiently.
Sealing the Tank
To prevent future damage and leaks, it’s essential to seal the repaired areas thoroughly:
1. Applying a Waterproof Sealant Inside and Outside the Tank
Choose a high-quality waterproof sealant suitable for masonry surfaces. Apply the sealant to both the inside and outside of the tank using a brush or roller. Ensure you cover all repaired areas and any potential weak spots.
2. Ensuring Even Coverage and Proper Drying Time
Make sure the sealant is applied evenly to avoid any weak points. Follow the manufacturer’s recommended drying time to ensure the sealant cures properly. This usually involves keeping the area dry and free from disturbance for a specified period.
By following this step-by-step guide, you can effectively repair your crawl space foundation and ensure it remains strong and stable for years to come. Remember, proper preparation and using the right materials are key to successful repairs.
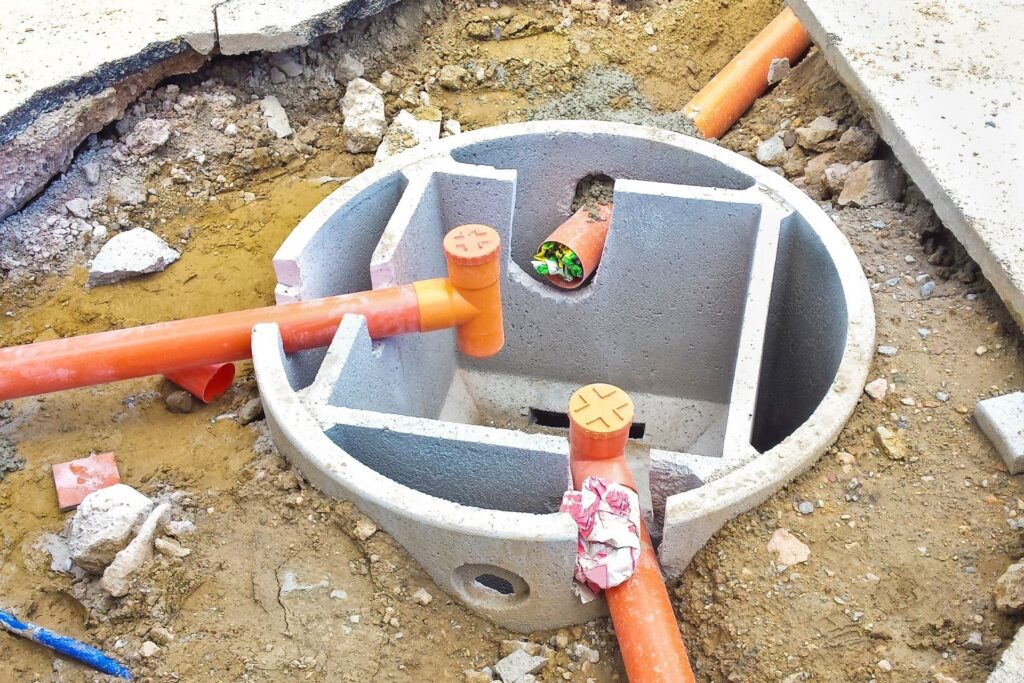
Post-Repair Maintenance
Proper post-repair maintenance of your water tank is crucial for ensuring its longevity and functionality. In this section, we’ll delve into the essentials of maintaining your tank after repairs, covering regular inspections and preventative measures.
Regular Inspections
Importance of Periodic Checks for New Leaks
Once your tank has been repaired, it’s essential to carry out regular inspections. These inspections are vital because they help identify any new leaks or weaknesses that may develop over time. Regular checks can save you from major repairs down the line, ensuring your tank remains in optimal condition. Leaks can often start small and go unnoticed until they cause significant damage, so catching them early is key to maintaining the integrity of your tank.
Tips on What to Look for During Inspections
During your inspections, there are several critical aspects to focus on:
Visible Signs of Leaks: Check for any signs of water around the tank’s base or on its surface. Even small puddles can indicate a problem.
Tank Surface: Look for cracks, rust, or any form of deterioration on the tank’s exterior. These can be early signs of structural weakness.
Connections and Fittings: Ensure that all connections, valves, and fittings are secure and free from corrosion or wear.
Water Quality: Sometimes, a change in the water quality, such as unusual color or odor, can be an indicator of internal issues within the tank.
Preventative Measures
Protecting the Tank from Environmental Damage
Taking proactive steps to protect your tank from environmental damage can significantly extend its lifespan. Here are some effective strategies:
Using Tank Covers and Protective Coatings
Applying a protective cover over your tank can shield it from harsh weather conditions, such as heavy rain, hail, and intense sunlight. Tank covers are especially useful for preventing debris from entering the tank and causing contamination or blockages. Additionally, protective coatings can be applied to the tank’s exterior to prevent rust and corrosion. These coatings act as a barrier against moisture and other environmental elements that could compromise the tank’s structure.
Managing the Surrounding Area to Prevent Damage
The area surrounding your tank plays a significant role in its maintenance. Here are some tips for managing this space effectively:
Clear Vegetation: Ensure that there are no plants or trees growing too close to the tank. Roots can interfere with the tank’s foundation, and falling branches can cause physical damage.
Drainage: Make sure that the area around the tank has proper drainage. Standing water can lead to rust and weaken the tank’s base.
Barriers and Fencing: Installing barriers or fencing around the tank can protect it from accidental impacts and unauthorized access. This is particularly important if the tank is located in an area prone to human or animal traffic.
By implementing these preventative measures and maintaining a regular inspection schedule, you can ensure that your water tank remains in excellent condition long after any repairs have been made. This proactive approach will not only save you money on future repairs but also ensure a consistent and reliable water supply.
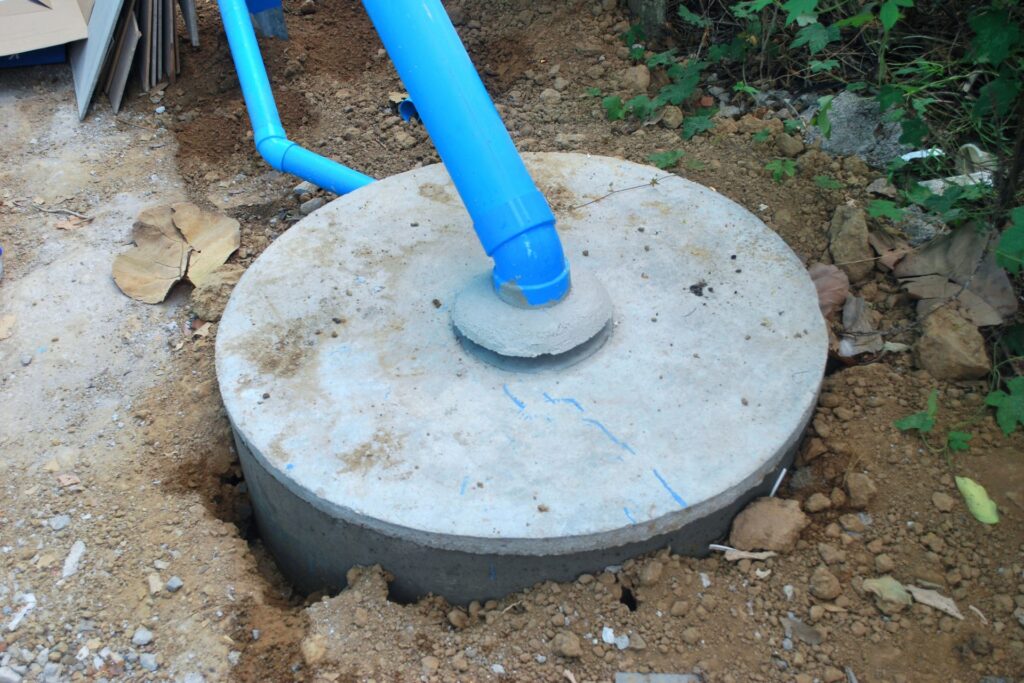
When To Call A Professional
Maintaining your home can often be a fulfilling and cost-effective endeavor, but knowing when to call in the professionals is crucial to avoid exacerbating issues. Here’s a detailed look at when to enlist expert help and how to find the right professional in New Zealand.
Complex Repairs
Recognizing When a Repair is Beyond DIY Capabilities
DIY projects can be a great way to learn new skills and save money. However, it’s essential to recognize your limits. Certain repairs can be too complex, dangerous, or critical for a DIY approach. Signs that a repair might be beyond your capabilities include:
Structural Damage: Cracks in the foundation or significant wall shifts indicate serious structural issues that require professional evaluation and repair.
Electrical Problems: Any issues involving electrical wiring, outlets, or circuit breakers should be handled by a licensed electrician to prevent hazards.
Plumbing Failures: Major leaks, sewer issues, or water heater problems often need the expertise of a professional plumber.
Roofing Issues: Significant leaks or damaged shingles can lead to more extensive problems if not addressed correctly. Roofing work is also risky due to height.
Types of Damage That Require Professional Intervention
When dealing with the following types of damage, it’s best to call a professional:
Water Damage: Persistent leaks or flooding can cause extensive damage to your home’s structure and promote mold growth. A professional can identify the source and properly mitigate the damage.
HVAC System Failures: Heating, ventilation, and air conditioning systems are complex. Professionals can diagnose issues and ensure the system runs efficiently.
Asbestos Removal: If your home has asbestos, professional removal is necessary to ensure safety.
Major Renovations: Large-scale remodeling projects often require building permits and adherence to local codes, making professional assistance essential.
Finding a Reliable Contractor in NZ
Tips for Choosing a Qualified Professional
Finding the right professional can seem daunting, but following these tips can help:
Verify Qualifications: Ensure the contractor is licensed and certified to perform the work. In New Zealand, you can check this through the Licensed Building Practitioners (LBP) register.
Experience and Specialization: Choose a contractor with experience in the specific type of repair or renovation you need. Specialization often means better quality work.
Insurance: Confirm that the contractor has adequate insurance coverage to protect against any damages or injuries that might occur during the project.
Questions to Ask Potential Contractors
When interviewing potential contractors, ask these key questions:
- What is your experience with this type of project? Understanding their experience helps gauge their expertise.
- Can you provide references from past clients? Talking to previous clients can give insights into the contractor’s reliability and quality of work.
- What is the estimated timeline and cost? Clear timelines and cost estimates help manage expectations and budgets.
- Do you offer a warranty or guarantee? A warranty on their work can provide peace of mind.
Importance of Checking Reviews and References
Before making a final decision, it’s crucial to:
Read Online Reviews: Check platforms like Google, Yelp, or trade-specific websites for reviews. Consistent positive feedback is a good sign.
Contact References: Speak directly with past clients to get a firsthand account of their experience with the contractor.
Check Professional Associations: Membership in professional organizations can indicate a commitment to industry standards and continuous education.
By knowing when to call a professional and how to find a reliable contractor, you can ensure your home repairs and renovations are completed safely and to a high standard. This approach not only protects your investment but also provides peace of mind, knowing the job is done right.
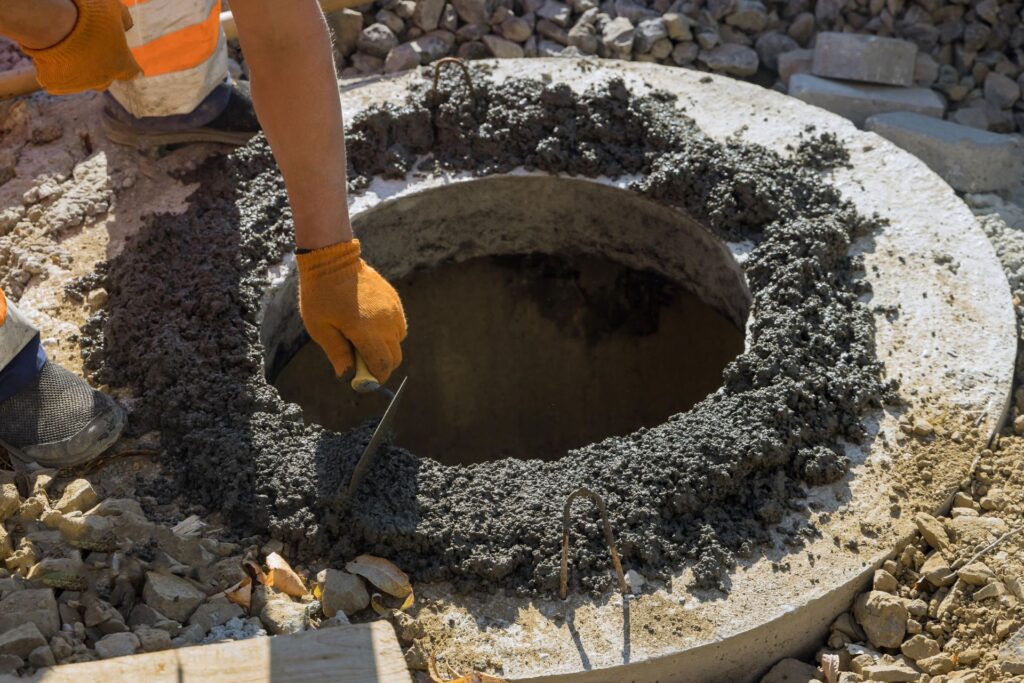
FAQs: About How To Fix Leaking Concrete Water Tank NZ
Concrete water tanks can leak due to various reasons such as cracks caused by age and weather, poor construction or installation, ground movement, and chemical reactions with water and soil.
You can identify a leak by looking for visible cracks, damp patches around the tank, reduced water levels without usage, mold or algae growth, and unusually high water bills.
Ensure the tank is empty and dry, wear protective gear like gloves and goggles, and ensure the work area is safe and accessible.
You’ll need tools like a hammer, chisel, and drill, and materials such as concrete patch mix, epoxy or polyurethane for deeper cracks, and a waterproof sealant.
Clean the affected area thoroughly by removing debris and loose material from cracks, and ensure the surface is dry before applying any repair materials.
Mix the concrete patch material, apply it to the small cracks, smooth the surface, and allow it to set according to the manufacturer’s instructions.
Chisel out larger cracks to create a clean surface, use epoxy or polyurethane injection for deeper cracks, and apply hydraulic cement for larger repairs.
Apply a waterproof sealant inside and outside the tank, ensuring even coverage. Allow the sealant to dry completely as per the product instructions.
Regularly inspect your tank for new leaks, protect it from environmental damage using covers and protective coatings, and manage the surrounding area to prevent damage.
If the damage is extensive, involves complex repairs, or if you’re unsure about the repair process, it’s best to hire a qualified professional. Look for a reliable contractor with good reviews and references.
Conclusion
In conclusion, maintaining and repairing your water tanks is crucial to ensure their longevity and efficiency. We’ve discussed key steps, including regular inspections, identifying early signs of wear, and the importance of timely repairs to prevent costly damage. Regular maintenance not only extends the life of your tanks but also safeguards your water supply from contamination. Don’t wait for minor issues to escalate into major problems; take proactive measures today. We urge you to inspect your tanks regularly and address any leaks or damages promptly. Ensuring the proper care of your water tanks is essential for a reliable and safe water storage system.
About the Author:
Mike Veail is a recognized digital marketing expert with over 6 years of experience in helping tradespeople and small businesses thrive online. A former quantity surveyor, Mike combines deep industry knowledge with hands-on expertise in SEO and Google Ads. His marketing strategies are tailored to the specific needs of the trades sector, helping businesses increase visibility and generate more leads through proven, ethical methods.
Mike has successfully partnered with numerous companies, establishing a track record of delivering measurable results. His work has been featured across various platforms that showcase his expertise in lead generation and online marketing for the trades sector.
Learn more about Mike's experience and services at https://theleadguy.online or follow him on social media: